Controller
Area Network (or CAN) is the latest communication system within the automotive
world. At its simplest level, it can be thought of as a means of linking
all of the electronic systems within a car together to allow them to communicate
with each other.
As computerisation
within a car increases, so to does the number of different electronic
systems. The information recorded and processed by each one is often used
by one or more others - hence the requirement for a standardised means
of quickly passing information between them. This requirement led to the
development of CAN.
Background
The CAN
technology was first developed by Bosch for industrial use, but was quickly
recognised as a powerful system for in-car use. Some manufacturers were
actually using the technology within their cars from as early as 1992,
e.g. Mercedes.
Which cars use the CAN protocol for diagnostics?
Within the
car diagnostics world, on certain 2003 and newer cars, it is possible
to access the CAN network (and communicate with various onboard systems)
through the 16-pin OBDII/EOBD diagnostics port. Prior to 2003, manufacturers
were required to provide non-CAN interfaces under the OBDII/EOBD legislation,
e.g. PWM, ISO etc.
Many of
these newer cars, e.g. Ford's latest range, Mazda RX-8, the latest Vauxhall
Vectra, offer only the CAN protocol/interface as a means of communicating
with the engine-management system. This will actually be mandatory on
all cars by 2008.
Whilst many
of these cars might still be under the manufacturer warranty, anyone investing
in diagnostic tools for the long term should ensure that their tools support
the CAN protocol.
The CAN
protocol now forms part of the OBDII and EOBD standards. Manufacturers
could begin implementing CAN for engine/emissions diagnostic purposes
in 2003 and must implement it by 2008.
What are the benefits of CAN-based diagnostics?
The CAN
protocols and interface run at roughly fifty times the speed of the earlier
OBDII/EOBD protocols. This speed improvement, combined with the addition
of new diagnostic parameters, will give technicians the ability to see
data faster and gain more information from newer cars than is currently
available.
The original
OBDII/EOBD protocols (J1850-PWM, J1850-VPW, ISO-9141 and ISO-14230) did
help reduce the number of tools required for engine/emissions fault diagnosis,
but by allowing 4 protocols there was still a great deal of confusion,
and over-complexity of tools.
Simplifying
this to a single protocol can only lead to reduce this confusion, and
the cost of diagnostic tools.
Which
diagnostic port pins are required for CAN?
The CAN
system uses pins 6 and 14 in the 16-pin diagnostic socket:
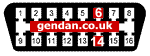
The
car will also need to have pins 4 and 5 (ground pins) and pin 16 (12 Volt
supply).
Which tools support CAN cars?
Nearly all of the tools we sell now support CAN.
The only exceptions to this are some of the lower-cost manufacturer-specific products, which are designed
to cover a specific range of vehicles - such as our VAG KKL cable.
Which cars currently support CAN?
A few examples
of 2003/4 model cars that require CAN-enabled tools are:
Ford Fiesta
Ford Focus
Ford Fusion
Ford Mondeo
Mazda 3
Mazda 6
Mazda RX-8
Porsche Cayenne
SAAB 9-3
Vauxhall Vectra
Most new
models from all manufacturers from approx. 2004 - CAN must be used for
EOBD engine diagnostics by all manufacturers by 2008.
|